I wrote this in 2023, and I have a 2024 update that’s worth reading after you finish this post.
There are a variety of wood varnishes available today, ranging from spar varnish to French polish.
When we first bought our small ski apartment in the mountains, the windows, batten-shutters, and balcony railings were (and still are) naturally light-coloured varnished wood.
The key is, and always has been, to maintain a good varnish protection on the wood exposed to the sun, rain and snow during the year, in particular for the balcony railings and the shutters.
My guess is that the original builders used some kind of polyurethane-based varnish in the 1970s. Over the last 40-odd years I’ve sanded down the shutters a couple of times and have continued to maintain the shutters using a transparent synthetic wood varnish (applied after a light sanding).
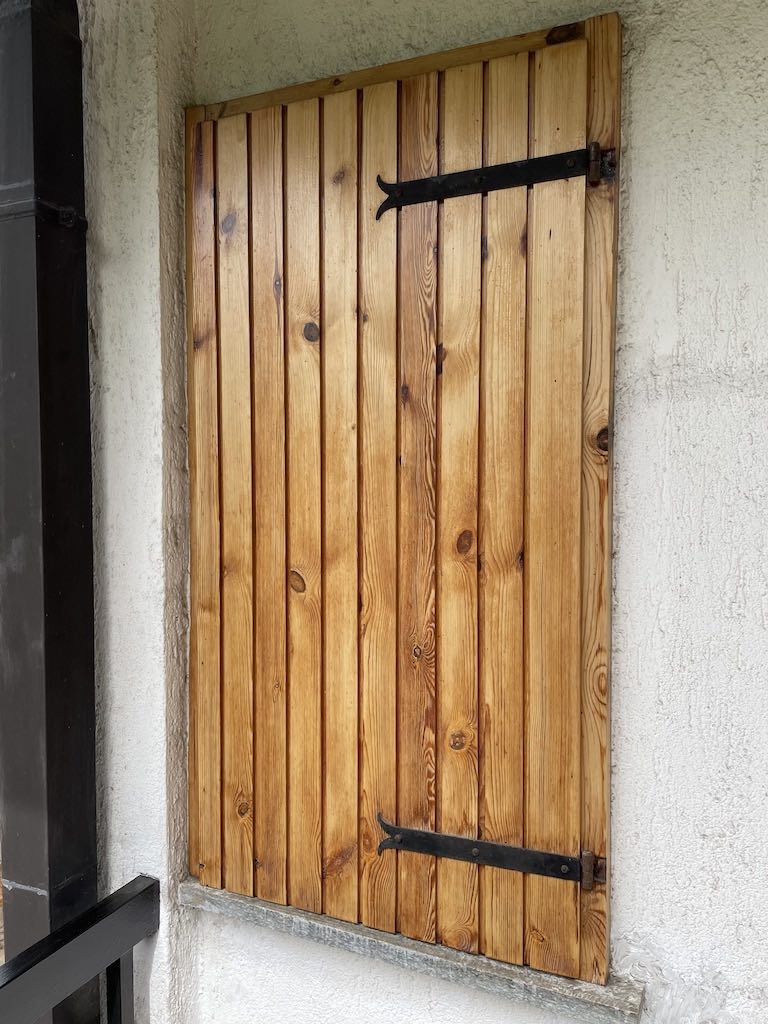
Balcony railings
The real challenge has always been the balcony railings. They are expose to the sun and rain during the entire year (plus snow in the winter).
Over the last 40-odd years we have tried every way to prepare and seal the wood with different types of varnish. The initial set of railings lasted well over 20 years, but I did once completely sand them down to fresh wood, before again sealing and varnishing them. The key was that we visited the apartment every summer, and would clean and re-varnish the railings annually.
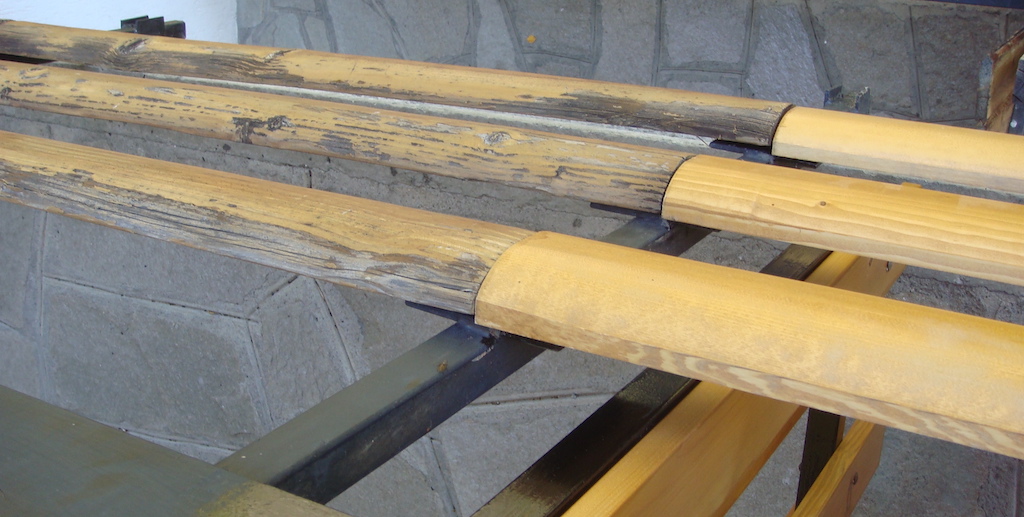
The reality was (less true today) that a new set of wood railings, treated, varnished, and fitted, was not that expensive.
The second set of wood balcony railings shown above (dating from 2008), were already three years old, and are set against the railings of our neighbours. Next door has only change once their wood railings in nearly 50 years, and they have never cleaned, treated or vanished them (idem for their shutters and windows).
This second set of railings lasted another 9 years, but there was a 4-year period when I was not able to regularly maintain them. This was fatal, and meant that we had to change the wood railings again in 2017.
A water-based varnish
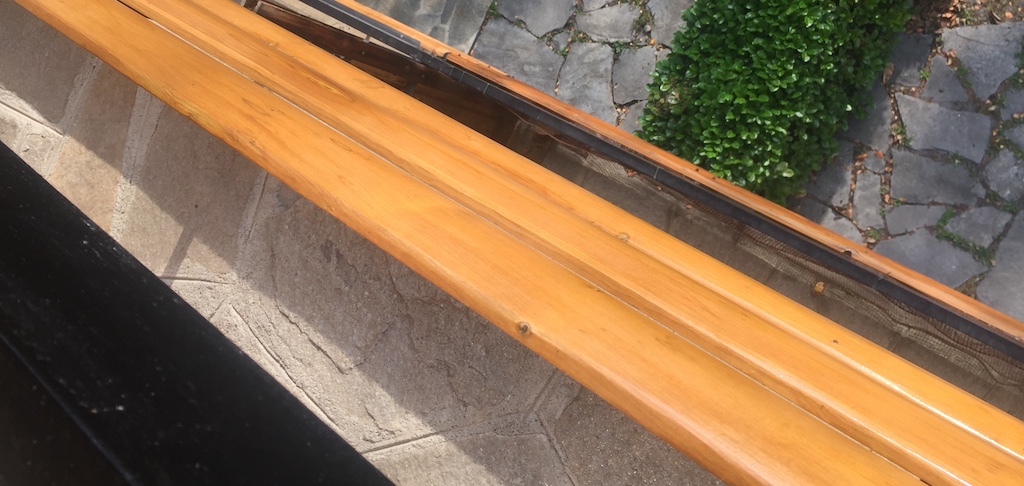
This time the new wood railings cost more than double the price of the last set, and a transparent water-based varnish was used.
The problem again was that we were not able to maintain the wood for 2 years (thanks to COVID), and in 2023 we now have the below wood railings, after sanding and varnishing.
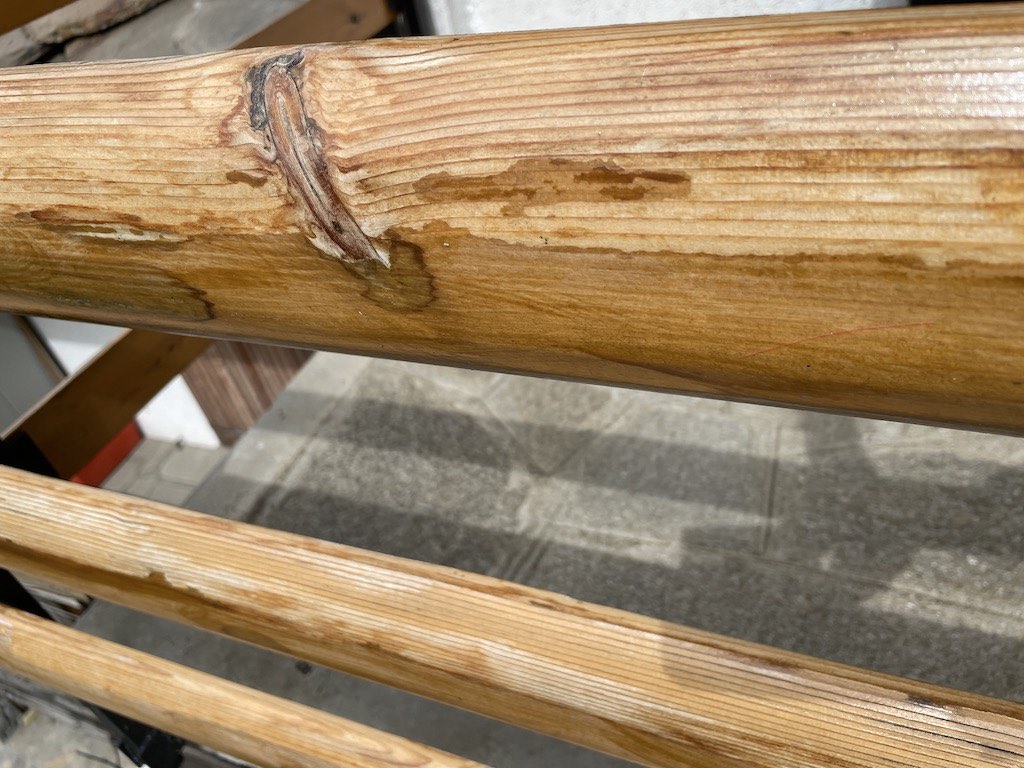
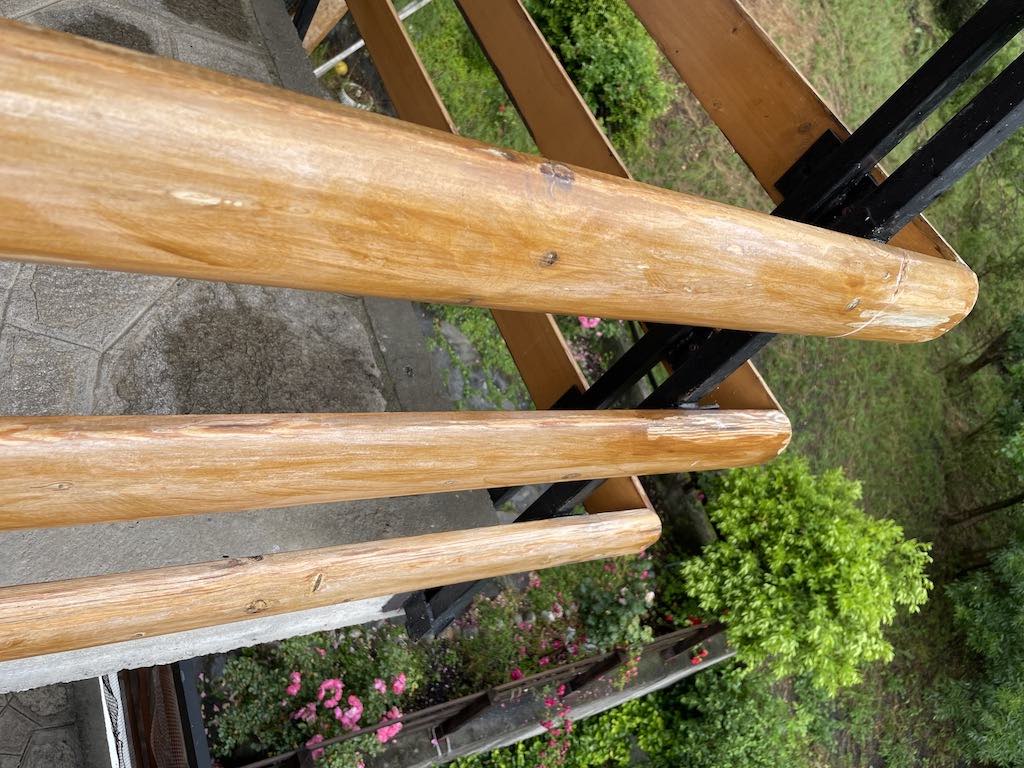
I understand perfectly the rational for using a water-based acrylic varnish:-
- Easy to apply, quick drying and non-hazardous.
- Environmentally friendly.
- Low odour.
- Usually has built in UV stabilisers and dry film biocides which make it ideal for outdoor applications, providing long lasting service and weather protection.
- Said to have excellent resistance to stains and repels water and moisture from penetrating the coating.
- Excellent adhesion to new and previously painted wood (I’m told you can’t mix different types of varnish).
We will see in a couple of years.
What exactly is a wood varnish?
- Wood varnish is in fact one type of ‘finish’, and refers to the film forming coatings applied to the surface of the wood to protect it and to highlight its appearance. There are four basic types of finishes used in woodworking:-
- Penetrating finishes
- Varnish (including polyurethane)
- Shellac, a resin secreted by the female lac bug
- Lacquer, most often made from resin extracted from trees.
Of the various types of finishes, the penetrating sealers are the easiest to use. Some of these sealers also contain a stain so that the wood can be stained and finished in one application. An advantage to using the penetrating oil finishes is that they are easy to restore, since the finish will never have to be stripped. The big disadvantage of these finishes is that a truly great finish may require 10 or more coats.
Varnishes are the standard for the home finishing market. They provide a tough, durable finish that is resistant to most household chemicals. The newer polyurethane varnishes are extremely durable, however, they may not be compatible with the stain, sealer or filler coats used and it not possible to rub the finish to obtain a particular lustre or gloss. Polyurethane, however, does come in a satin and high gloss finish. All varnishes are relatively easy to use, but it’s important to never use an exterior finish varnish for interior uses as it never dries completely.
Traditionally oil varnishes were the most common. This included spar, interior, floor (usually urethane), rubbing varnishes, etc., which contained a fixed or fatty oil, in addition to a volatile solvent and often a resin. Fatty oils were usually either:-
- Linseed Oil, is practically always refined or treated in various ways and was often called “varnish oil”, “borate oil” (boiled oil prepared by heating with manganese borate), etc. The reality was that linseed oil was used by traditional craftsmen simply because it was easily available and cheap. Better craftsman of the period used shellac when possible. However, a linseed oil finish is too thin and soft to protect well against heat, stains, or wear.
- Tung Oil, must be treated to remove or prevent gelatination (formation of a jelly-like mass) which ordinarily occurs when the oil is heated. A common method for treating tung oil was to add rosin, which has a solvent action on the jelly-like material.
- Castor and Safflower oils can also be used.
The chief volatile thinners used in the manufacture of varnish were turpentine, and mineral spirits (sometimes called spirit oils). Many spirit varnishes, especially shellac varnish, contain either grain (ethyl) alcohol, wood (methyl) alcohol, or denatured alcohol (a mixture of grain alcohol with such materials as wood alcohol, acetone, pyridine, benzine, etc.). Metallic driers were used such as lead, manganese, cobalt, etc. They were used in the manufacture of both paints and varnishes.
Shellac forms a hard, tough finish but it is not resistant to water or alcohol. White spots will form when water comes in contact with a shellac finish. It is however, easy to apply and works good as a sealer or even a finish coat where water and alcohol resistance is not important.
The fourth type of finish used on furniture is lacquer. The lacquer finishes are very tough, hard, and durable but are difficult to apply. Lacquers are really formulated for spraying operations.
Traditionally a water-resisting spar varnish was the general utility varnish, suitable for both outside and inside exposure, where durability was the chief requisite.
Modern wood varnishes contain synthetic resins such as polyurethane, and are heat-resistant, waterproof and hardwearing. Marin or ‘yacht varnish’ withstands exposure to salt water. Solvent-based paints for wood are made from solid pigments suspended in a synthetic resin, such as alkyd, vinyl, acrylic, urea or polyurethane, mixed with oil. Additives make it glossy, matte, satin, fast-drying, etc.
What's so special about a water-based finish?
Water-based finishes are highly touted by manufacturers for their scratch resistance. They are very tough finishes, resembling solvent-based polyurethane. But they differ from solvent-based polyurethane in almost every other respect. Water-based finishes are less resistant to heat, solvents, acids, or alkalis, and they provide a weaker barrier against water penetration and water-vapour exchange.
This is not to say that water-based finishes are not good finishes, only that film toughness isn’t everything. A hot coffee cup, a little bit of fingernail polish remover, or a washing with an alkali soap will cause damage. Also the finish won’t do much to stop wood from moving with humidity changes compared to solvent-based polyurethane.
Latex paint, which is chemically related to a clear water-base varnish, is valued for use on the outside of houses precisely because of its ability to ‘breathe’, or let water vapour pass through.
Water-based finishes differ from all solvent-based finishes in the following respects:-
- They have reduced solvent content.
- They clean up with water.
- The cured finish is colorless.
Water-based finishes contain very little solvent compared to solvent-based finishes. There is therefore less solvent to evaporate into the atmosphere and cause pollution, less solvent to fuel a fire, and less solvent to breathe. Though reducing air pollution was the rationale for the introduction of water-based finishes, however reduced fire and health hazards are of more immediate benefit.
Like latex paint, water-based finishes are relatively easy to clean up. It’s easy to wash brushes or spray guns in water before the finish begins to cure. Lacquer thinner, acetone, toluene, and xylene will all dissolve water-based finishes.
Water-base finishes are colorless. On certain surfaces, such as light-colored and pickled (white-stained) woods, a colourless finish is desirable. But lack of colour causes darker woods, such as walnut and mahogany, to look washed out and lifeless. Of course woods can be stained or dyed before applying the finish.
Substituting water for most of the solvent is great for preserving the environment but can cause a number of problems, including ‘grain raising‘, which occurs anytime water is put on wood.
Water is far more weather-sensitive than solvents. The curing time of water-based finishes varies much more in different weather conditions than the curing time of other finishes. On warm, dry days water base will usually dry rapidly enough to preclude dust problems. On cool or humid days the finish may take quite some time and therefore is more difficult to keep dust-free.
A finish protects the wood by slowing the penetration of water and the exchange of water vapour. Resistance to water penetration is important when choosing a finish. Resistance to water-vapour exchange is one of the most important functions a finish performs on any wood object. Excessive water-vapour exchange between the wood and the atmosphere causes splits, warps, and joint failure.
Resistance to water and water vapour depends as much on the thickness of the finish as it does on the type of finish. The three types of varnish (alkyd, phenolic, and polyurethane), which are nearly impermeable to water and water vapour when built up to a thick film, lose almost all of their resistance when too thinly applied.
Among the film finishes, the best water and water-vapour protection is provided by varnish and conversion finishes. The least water-vapour-resistant finishes are lacquer and water-base varnishes.
Delving a bit deeper it would appear that it’s a mistake to think of the two cans, resin-varnish and water-based varnish, as two totally different products. Varnish, a resinous film former, was, and continues to be, made from various types of plant-based oils. And these oils are mixed with metals and different types of spirit oils to help the resin level and dry.
The idea is that oil and water, by nature, do not mix. However, it is in fact possible to neutralise the oil resin and add water-soluble solvents, which remain in suspension! Certain emulsifiers are used to ‘mix’ the oil and water, in particular dipropylene-dimethyl-ether.
In fact most water-based varnish formulators don’t mention what natural oil is being used in their products, but the resin is usually based on tung, linseed, or castor oil. The water-based varnish I used just mentioned that it included an anti-fungal.
Conclusion
Water-based have many advantages, namely:-
- Water-based products helps the finish build faster, thus requiring fewer coats.
- Water-based products really are nonflammable.
- Water-based finishes do contain small amounts of toxic solvents, the amount is insignificant when compared with traditional finishes.
- Water-based finishes is that they dry fast, especially when compared with brushable varnishes and polyurethanes.
- Water-based finishes have exceptional clarity making them the ideal choice to protect the wood but not change its colour.
- The resins used in water-based finishes have improved to the point where most products are at least as durable, if not more so, than solvent-based materials.
- The cleaning solvent for water-based finishes is simply warm, soapy water.
- Water-based finishes actively shield and protect the wood surface from the attack of sunlight, which often causes the conventual vanish films to crack and peel off. it makes wood water-repellent by retaining its elasticity and breathability.
So, plenty of reasons for paintshops to use water-based products.
However, the biggest cause for concern when using water-based finishes is the weather. Water-based finishes dry fast under ideal conditions, but are far less reliable in high humidity and cold situations. Water-based finishes raise the grain and need more sanding than with a traditional, solvent-based finish. Water-based products are not compatibility with oil-based product, including fillers, stains, dyes, and other topcoats.
Professionals see water-based varnishes as wonderful when spray-applied. They are not flammable and don’t emit toxic fumes, etc. A well chosen water-based varnish will offer excellent durability, lustre and a look/feel that matches-up with old world varnishes in restoration or new construction applications.
As a customer, you just have to hope that the professional, is just that, professional.
And when I have bought a tin of water-based varnish, it alway turns out to be from a different company, and with a label providing virtually no useful information about its contents. I sand the wood, re-varnish, and hope for the best (and expect the worst).
A final word on brushes
When buying the varnish, I also picked up a brush. It turned out to be an excellent brush for this job. The brush was a size 30 ‘flat’ from the Italian ‘pennellificio‘ (brush manufacturer) ARTE, and used nylon or polyester ‘hairs’. It was really easy to use, and to clean. Well worth a mention.
References
Andy Charron, “Water-Based Finishes“
Bob Flexner “Understanding Wood Finishing“
I was particularly impressed with the tips, etc. provided by Jeff Weiss of TargetCoatings