Driving back home one Sunday morning I passed by a newly installed wind turbine. And I was a bit surprised that I could drive right up to the tower, even if it had not yet been commissioned.
I’ve always been attracted to new technology, and here was a chance to “get up close” to a tower.
Check out these videos:-
Soler.lu – Wind Farm Duelem – Wind Turbine Assembly – Part 1
Soler.lu – Wind Farm Duelem – Bladelifter – Part 2
And check out also these background videos:-
How Wind Turbines Really Work: The Hidden Secrets
Wandpark Duelem
Wandpark Duelem is the local name for the Dalheim Wind Farm, where Dalheim is a a small commune and village in south-eastern Luxembourg.
The wind farm consists of five wind turbines with a power installed total of 21 MW, which made it (2024) the largest wind farm in the south of Luxembourg.
The annual production of energy is estimated at 36.6 GWh, which corresponds to the consumption of 8,133 families of four people or of 32,532 individuals (remembering that the village of Dalheim only had 2,405 residents in 2022). This represents an annual saving of 23,000 tonnes carbon-dioxide (1 tonne = 1,000 kg).
As part of the development of the project, various environmental measures were implemented, in particular to protect local wildlife. The measures included, for example, planting fruit trees and hedgerows to distract and protect bats, creating flower strips as a habitat for the skylark during its breeding season, installing perches for the buzzard to help it hunt, using staggered mowing to create a hunting and refuge area for the red kite, black kite and buzzard, creating islets of old woodland for cave bats and creating bodies of water and watercourses as a preserved and valuable habitat for bats. During the operation of the wind farms, occasional shutdowns are also planned to protect bats and red kites.
What makes up one wind turbine?
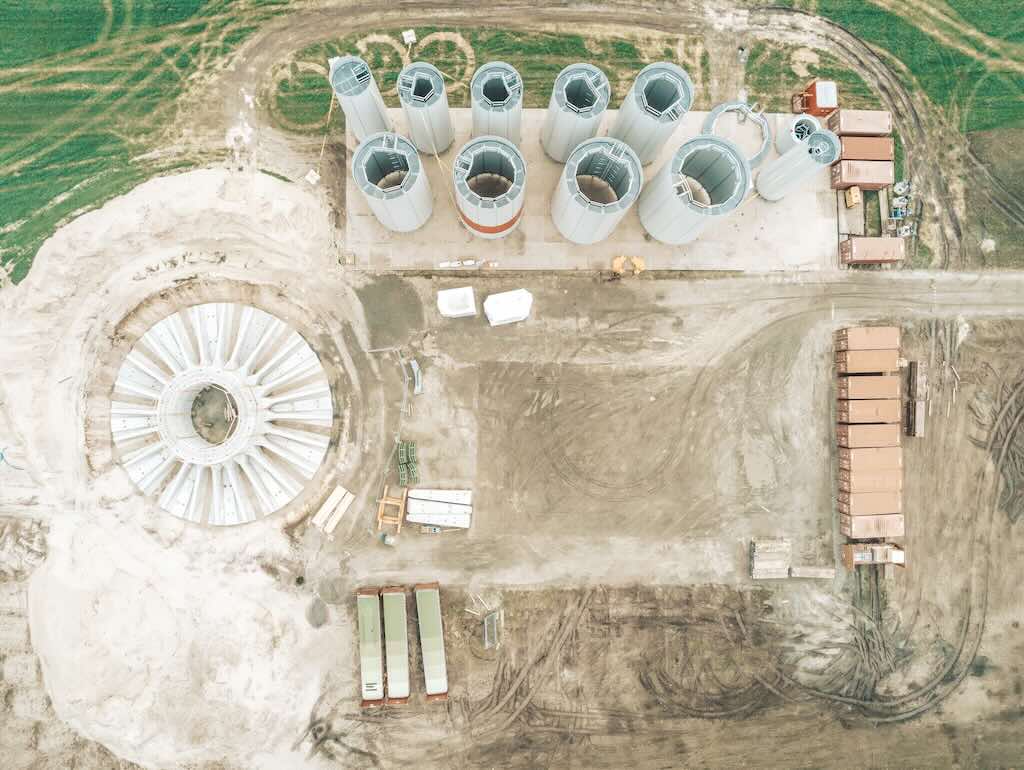
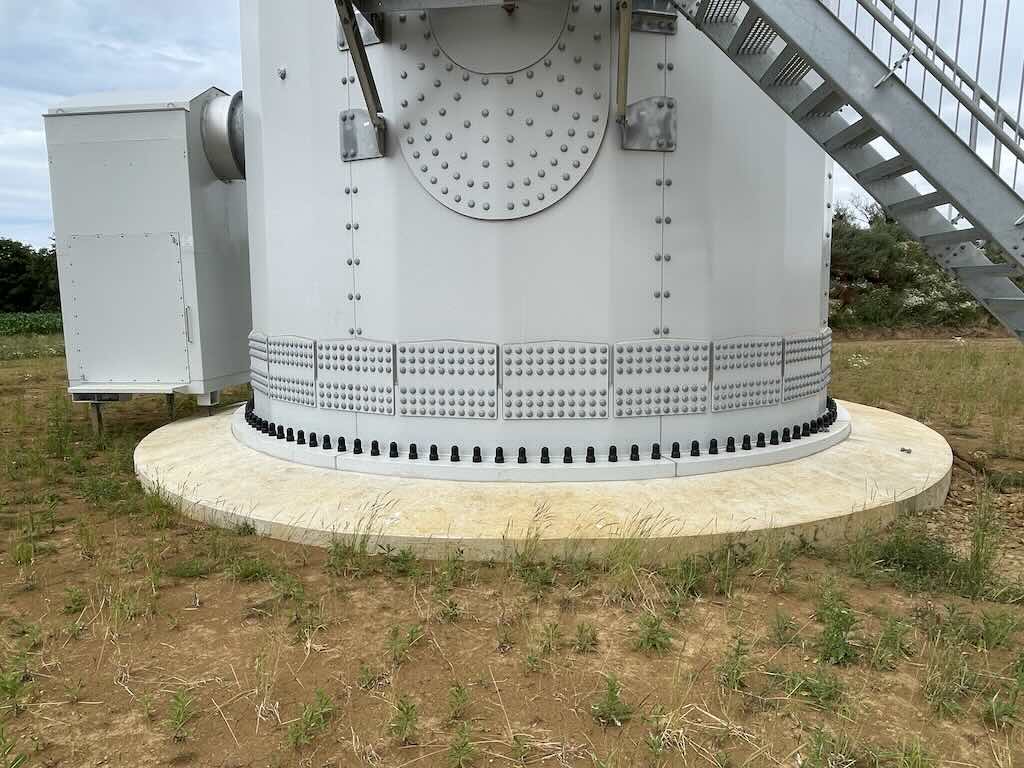
Foundations
It starts with a precast ribbed concrete and steel base with a total weight of +/- 1650 tonnes. That’s 90.3 tonnes of steel and 624 cubic metres of concrete. The base has a diameter 23 metres underground and 8.6 metres on the surface, deep 2.7 metres. So the two important things is that there is no casting-in-place (onsite), and that what you see on the surface is just a small part of the mass sitting underground.
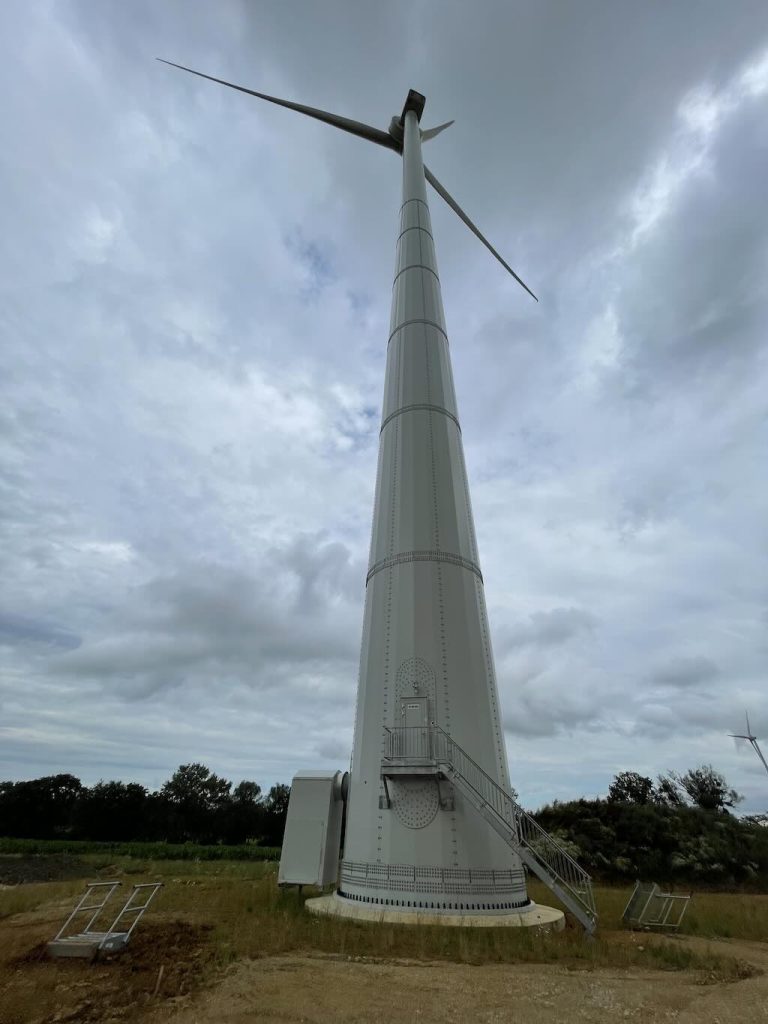
Tower
This is a 149 metre hybrid steel tower made up of six sections, plus three finished steel sections on top. The first six sections are each 11.5 metres tall and weight between 41 and 57 tons per section. The three top sections are 60 tons each, and are between 20 and 28.5 metres tall. The diameter at the bottom is 6.9 metres and on the top 3.2 metres. The total weight is 500 tons.
A hybrid tower means it’s made of precast concrete parts with a steel section or a tubular steel top tower. All towers are already provided with the finished paint or weather and corrosion protection in the factory, so that after assembly, apart from repairing defects and possible transport damage, no further work is required. As standard, the exterior paint is colour-graded in the lower part (the colour gradation can optionally be omitted).
The steel tower is a tube made of sheet steel that tapers linearly towards the top. It is prefabricated in the factory in a few large sections. Flanges with holes for assembly are welded to the ends of the sections. The tower sections are placed on top of each other at the installation site and screwed together. The connection to the foundation is made using a foundation basket. The hybrid tower is assembled from the precast concrete parts at the installation site. The segments are usually placed on top of each other dry, but a mortar leveling layer can also be applied. The vertical joints are connected by a screw connection. The upper steel sections are then placed on top and screwed in place.

Blade
There are three blades, each 56.5 metres long and weighing 19.9 tons. And as you might guess, they are not the easiest things to transport to rural sites. The special transporters are rare, and are able to move the blade up-down and side-to-side to navigate local villages and narrow roads. A single wind turbine can cost between $2.6 to $4 million, whereas the total material and labour costs of fabricating a single blade has been quotes at anywhere between $130,000 and $600,000 (I guess depending upon size). The transport of a single blade can cost between $30,000 and $100,000 depending upon distance (off-shore it can cost upto $150,000 per blade).
The blades are made of glass fibre reinforced plastic (GRP or glass fibre and epoxy resin), balsa wood and foam, and have a significant influence on the yield of the wind turbine and on its noise emissions. The rotor blade is manufactured using a half-shell and vacuum infusion construction. For this particular model of turbine (E-115 EP3 E3) the blades are specially designed for operation with variable blade adjustment and variable speed. The polyurethane-based surface coating protects the rotor blades from environmental damage such as UV radiation and erosion. The coating is very abrasion-resistant and tough.
The three blades are each adjusted by independent microprocessor-controlled blade adjustment units. The set blade angle is constantly checked using 2 blade angle measurements each and the 3 blade angles are synchronised with each other. This enables the blade angles to be set quickly and precisely in accordance with the prevailing wind conditions.
The blades are also optionally (or sometimes also equipped as standard) with a serrated profile in a section of the trailing edge of the blade. This trailing edge serration reduces the turbulence at the trailing edge of the blade and thus reduces the noise emissions of the wind turbine.
The interior of the rotor blades is equipped with vortex generators on the suction side. The vortex generators delay the separation of the boundary layer flow from the rotor blade surface. The aerodynamic properties of the wind turbine are therefore less sensitive to temporary surface changes and wind conditions. The performance of the wind turbine increases and the noise emissions decrease.
The blade adjustment changes the angle of attack at which the air flows against the blade profile. The blade angle changes the lift of the rotor blade and thus also the force with which the blade turns the rotor. In normal operation (automatic operation), the blade angle is set so that, on the one hand, the energy contained in the wind is used optimally and, on the other hand, the wind turbine is not overloaded. The blade adjustment also enables the rotor to be aerodynamically braked. If the wind turbine reaches its nominal power, the blade adjustment turns the rotor blades just far enough out of the wind as the wind speed continues to increase so that the rotor speed and the power absorbed by the wind and converted by the generator do not exceed the nominal values or only exceed them insignificantly.
With nominal or above the nominal wind speed, the wind turbine maintains the speed of the rotor at its target value (approx. 12.7 (2990 kW)/13.2 (4200 kW) rpm) by adjusting the blades and thereby limiting the power to its nominal range of 2990/4200 kW. In addition there is a storm control which enables the system to operate even at very high wind speeds, but with reduced rotor speed and power. As the wind speed continues to rise, the rotor blades can be turned, and at wind speeds above 34 m/s (10-minute average), the rotor blades are almost in the “feather” position. The wind turbine runs in spin mode without outputting power, but remains connected to the receiving power grid. When the wind speed drops below 34 m/s, the turbine starts feeding in power again.
At wind speeds below 2.5 m/s, no electricity can be fed into the grid. The wind turbine runs in spin mode, i.e. the rotor blades are largely turned out of the wind (blade angle ≥ 60°), and the rotor rotates slowly or stops completely when there is no wind at all. Due to the slow movement (spin), the rotor bearings are less stressed than if they were at a standstill for a longer period of time, and electricity generation and feeding can be resumed more quickly when the wind gets stronger again.
Just as a “fun fact” below we have a newly designed 110 metre long aircraft for transporting wind turbine blades (planned for 2027). It is planned to have 12 times the capacity of a Boeing 747 and be 80 times larger than even the biggest military planes.
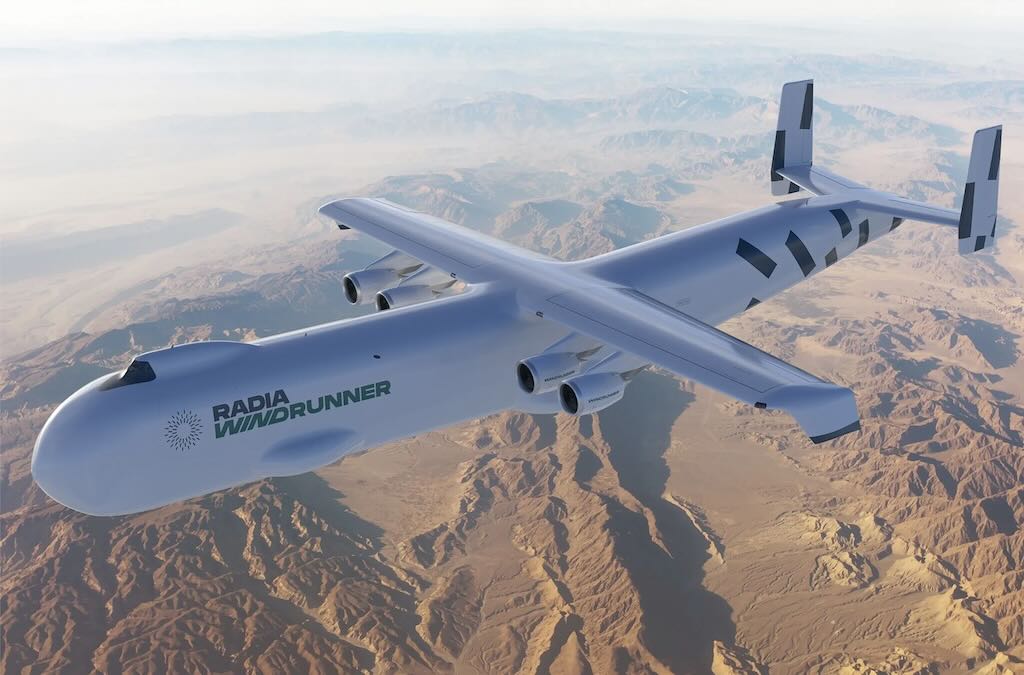
Back to reality, below we can see a blade being inserted into a nacelle.
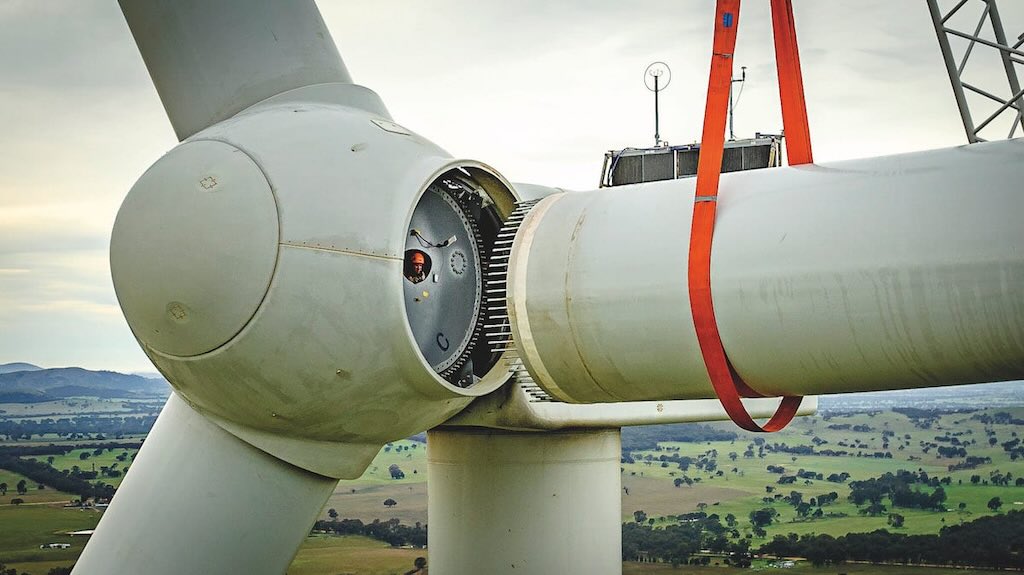
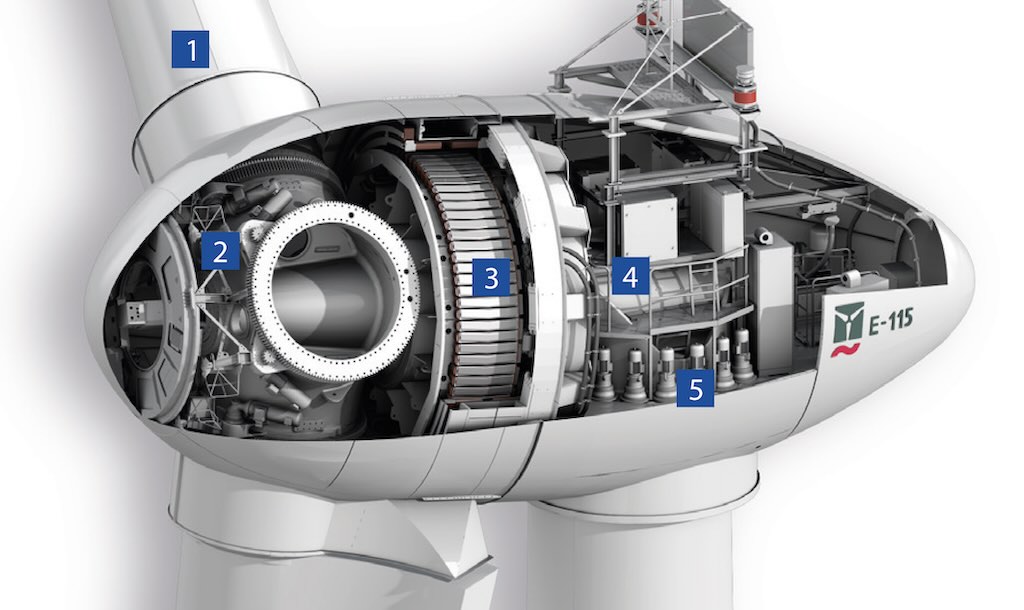
On the above simplified diagram, (1) is the Rotor blade, (2) Rotor hub, (3) Ring generator (4) Machine carrier, and (5) the Azimuth drive.
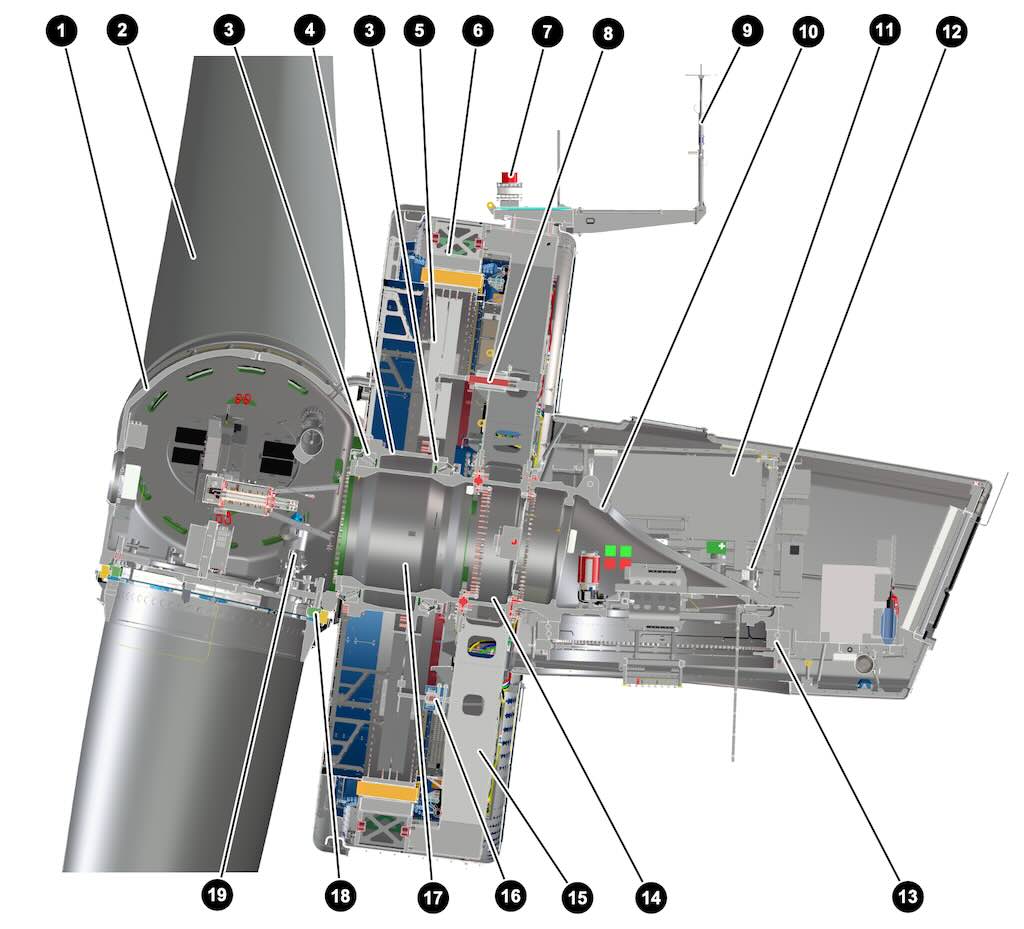
Components of the E-115 EP3 E3 are (1) Rotor hub, (2) Rotor blade, (3) Rotor bearing, (4) Rotor carrier, (5) Generator rotor, (6) Generator stator, (7) Lighting (optional), (8) Rotor lock, (9) Anemometer with lightning rods, (10) Machine carrier, (11) Nacelle control cabinet, (12) Azimuth drive, (13) Azimuth bearing, (14) Stator support star, (15) Support arm, (16) Rotor holding brake, (17) Spindle (18) Blade flange bearing, and (19) the Blade pitch drive.
The rotor hub rotates on 2 rotor bearings around a fixed axle. The rotor blades and the generator rotor, among other things, are attached to the rotor hub. The slip ring transmitter is located at the tip of the axle-journal (journals are support sections of the shaft and the axle). It transmits electrical energy and data between the fixed and rotating parts of the nacelle via sliding contacts.
The supporting element of the fixed generator stator is the stator carrier with 6 support arms. The stator carrier is firmly connected to the machine carrier via the stator support star. The stator ring with the aluminum windings in which the electrical current is induced is attached to the ends of the support arms.
The machine carrier is the central supporting element of the nacelle. All parts of the rotor and the generator are attached to it directly or indirectly. The machine carrier is rotatably mounted on the tower head via the azimuth bearing. The entire nacelle can be rotated using the azimuth drives so that the rotor is always optimally aligned with the wind.
The cladding is made of glass fibre reinforced plastic (GRP). It is made from several sections and is attached to the generator stator and the platform using steel profiles.
The 77.9 ton stator is the stationary part of a rotary system, so the part that converts the rotating magnetic field to electric current.
This particular type of wind turbine uses a high-pole, separately excited synchronous generator (ring generator). To make the best use of the wind energy potential at all wind speeds, so the wind turbine operates at variable speeds. As a result, the ring generator produces alternating current with fluctuating voltage, frequency and amplitude.
The windings in the stator of the ring generator form several independent three-phase alternating current systems. These systems are rectified separately from one another in the tower base and then converted back into three-phase current with a voltage, frequency and phase position that is in line with the grid by the inverters. As a result, the ring generator is not directly connected to the power grid of the energy supply company, but is decoupled from the grid by the converter.
The 69.1 ton rotor is the moving component in the generator.
Hub
The 39.1 ton hub is the part that holds the blades and connects them to the rotor.
The turbine is the name for the entire rotary mechanical device. In this particular wind farm they are Enercon E-115 EP3 E3, and each has a total weight of +/- 771 tons.
Grid feed-in system
The ring generator is connected to the grid via a grid feed-in system. This system essentially consists of a modular rectifier and inverter system, each with a common DC intermediate circuit.
The decoupling of the ring generator and the grid means that the power generated can be optimally transmitted. Abrupt changes in wind speed result in a controlled change in the power fed into the grid. Similarly, any disturbances in the electrical grid have practically no effect on the mechanical side of the wind turbine.
Crane
Without specialist cranes it would be impossible to build a wind turbine.
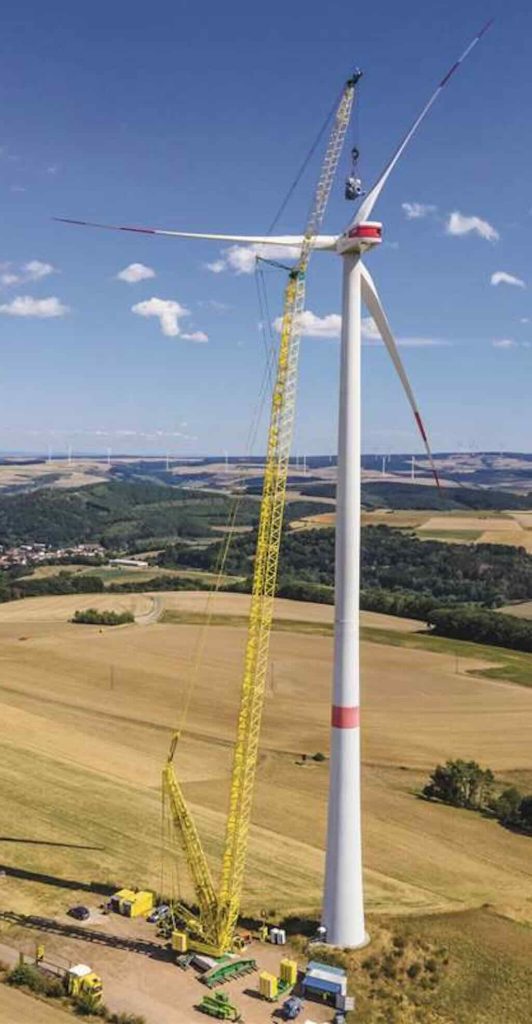
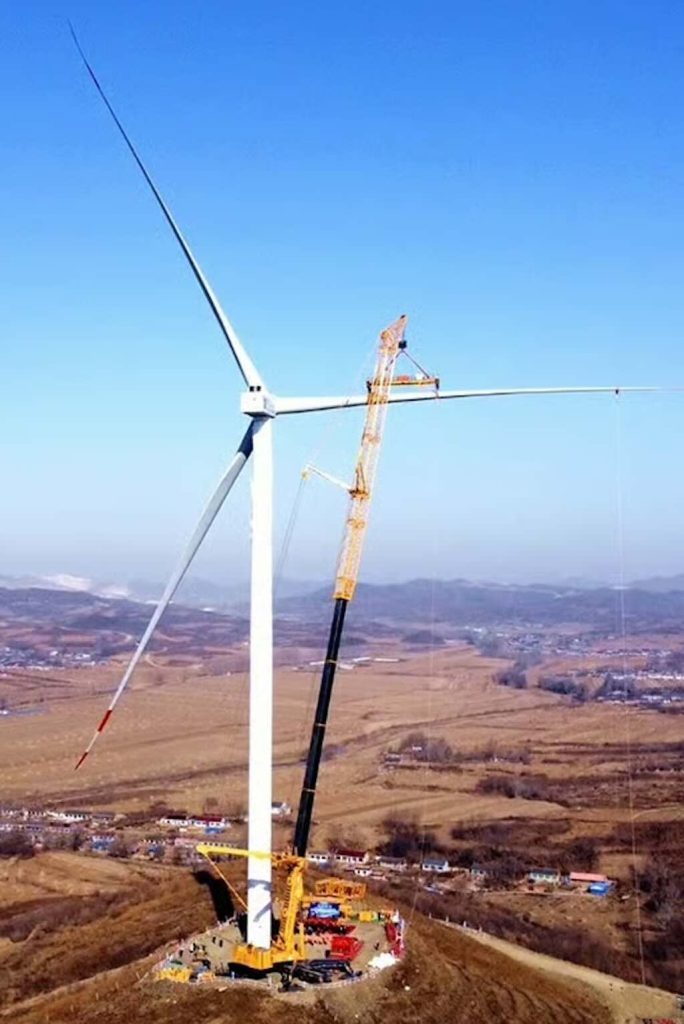
Who owns the Dalheim wind farm?
SEO (Société Électrique de l’Our) and Enovos Luxembourg each hold half of the shares in the public limited company Soler (Société Luxembourgeoise des Energies Renouvelables SA), founded in 2001.
In addition to operating three hydroelectric power plants, Soler continues to plan, build and operate wind turbines. After the wind turbines currently under construction have been commissioned, Soler will operate ten wind farms by the end of 2023 with a total of 48 wind turbines and a total installed capacity of 151.4 MW and an average annual production of more than 330 GWh.
In collaboration with the municipalities, Soler is currently developing other wind farm projects in Luxembourg or carrying out “repowerings” in the oldest wind farms.
And the cost?
There are a lot of unknowns, and a lot of pro- and anti-wind-farm “data”.
The costs for a utility scale wind turbine farm can range from about $1.3 million to $2.2 million per MW of nameplate capacity installed. Most of the commercial-scale turbines installed today are 2 MW in size and cost roughly $3-$4 million installed.
I don’t think that the above cost includes the leasing of land. But it is often argued that the cost of rural real estate is negligible, and fighting complaints in court costs more. And farmers may still use 95% of their land, as turbines need to be spaced out to best exploit the local wind dynamics.
Wind or solar does not use fuel, so the cost of the electricity is mostly determined by the capital cost amortised over the life of the plant. That in turn depends on the interest rate or discount factor. That factor is dramatically better due to the guaranteed 25-year life-time contract.
Subtracting subsidies, renewable electricity, wind or solar, can cost as much as $80 per megawatt hour. Such comparisons are still dubious because there are no unsubsidised, utility-scale wind or solar plants. Naturally no utility would buy $80 renewable electricity to replace fossil fuel electricity that can cost as low as $15 per megawatt hour. A stand-alone, unsubsidised enterprise wind or solar plant would be an economic failure because there would be no market for the overpriced electricity.
It is also not clear that renewable electricity is the most economic method for reducing carbon-dioxide emissions. However many authorities (states, countries, etc.) are required by law to have a renewable portfolio. The consequence of the law-mandate is that the utility has to grant whatever terms are required to convince investors to build the renewable power plants. In practice this results in the utility promising to purchase all the power generated for 25 years at a fixed rate. Forcing utilities to buy renewable power puts the suppliers of renewable power in an advantageous position.
The reduction in the cost from $80 to $25 includes explicit subsidies, advantageous financing conditions, and lower required rate of return that results from having a 25-year contract in hand from a credit worthy utility. There can also be tax credits that pays up to 30% of the plants cost.
Even when $25 per megawatt hour is touted in the press, wind or solar is far from competitive. The gap between $80 and $25 is accounted for by subsidies. The $10 difference between $25 and $15 is also a kind of indirect subsidy because the purchaser is paying $25 for the electricity that could have been generated in a backup fossil fuel plant, that already exists, for $15.
Of course adding wind or solar electricity reduces fuel consumption in backup fossil fuel plants. This saving in fuel amounts to about $15 per megawatt hour, the
cost of natural gas to generate a megawatt hour of electricity. The cost of coal is similar. The backup fossil-fuel plant still has to have its full staff and may have more costly maintenance due to the up-down style of operation forced by modern-day erratic energy consumption patterns. Maintenance of a wind farm is about $60,000 annually per turbine.
Still today the big picture is that when wind or solar is added to a grid it is supplemental power. Coal or gas plants are not necessarily eliminated. Those plants may have to stay in place to handle periods when wind and solar are not producing electricity. This does not stop claims that wind or solar is replacing fossil fuel, but it is fuel that is replaced, not necessarily the fossil-fuel plants. When wind or solar is producing, the fossil fuel plants are throttled back and they use less fuel. If, for example, a coal plant was closed when wind was added to the grid, the safety margin might be compromised. Blackouts are very expensive for society, so grid operators want to ensure that they have spare capacity sufficient to meet the largest demand peaks even when some plants are out of commission. Plants in spinning reserve status stand by ready to take over if a plant trips (breaks down). Injecting erratic electricity into the grid means that other plants also have to seesaw output to balance the ups and downs of wind or solar.
On the other hand other sources of electricity are also subsidised, but those subsidies are often better hidden. Global fossil fuels subsidies are, so the IMF has estimated, $5.2 trillion annually. This includes harmful effects of pollution to human health. For example, in Germany, coal fired plants cause approximately 4,000 premature deaths per year just from lung disease alone, from particulate matter. Then there are deaths caused by the mercury emissions and radioactive isotopes. That’s beside the cost incurred by carbon-dioxide emissions and climate change, or from mining coal in the first place. The cost to German public health is estimated at between €2.5 and €6.5 billion annually.
And finally we won’t mention the cost of end-of-life recyclability of different energy plants.